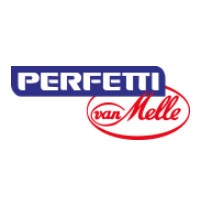
CI/TPM Operations Manager
CÔNG TY TNHH PERFETTI VAN MELLE (VIỆT NAM)
Địa điểm làm việc: Bình Dương
Hết hạn: 15/10/2023
- Chi tiết công việc
- Giới thiệu công ty
Vị trí công việc này hiện tại đã hết hạn nộp hồ sơ, bạn có thể tham khảo thêm một số công việc liên quan phía dưới
Mô tả công việc
1. BASIC PURPOSE OF THE POSITION
• Engage in the continuous improvement effort to improve safety performance, product quality, unit cost, and employee performance, utilizing a participative team approach.
• The ability to apply sound business analysis techniques to a situation. Identify and adapt to new opportunities and find easier success. Helping business implement technology solutions in a cost-effective way by determining the requirements of a project or program, and communicate them clearly to stakeholders, facilitators, and partners.
• Developing technical solutions to business problems, or to advance the company's manufacturing performance efforts with defining, analysing, and documenting requirements.
• Involve in the design or review of test cases, process change requests, and manage a project's scope, acceptance, installation, and deployment.
• React quickly to rapidly changing conditions and processes by eliminating defects and enhancing quality while achieving and maintaining optimal levels of process performance.
• Improving the outcomes of various processes so that, by mapping all the inputs and outputs of a defined business process, the incumbent can recommend ways to improve efficiency, reduce cost and /or increase customer satisfaction. Working with front-line staff, identifying improvement opportunities, and coaching employees on how to work more efficiently. Participates in the implementation of the continuous-improvement program.
• Improves policies, procedures, and processes, manages the continuous-improvement program, advises, and assists front-line staff.
• Coordinate and work on the PPE Project with external consultants in coordination with Group.
• Contribute to the required Centurion CSR project, including coordination on the EMP (Environment Master Plan) with the region by working closely with local Sustainability Team.
• Contribute to improvements in cost, cash, quality, responsiveness, and time to market to support profitable growth of the business.
• Ensure definition and implementation of lagging and leading performance indicators and periodical reporting of actual performance against these indicators to facilitate timely decision taking.
• Ensure continuous improvement of Operating Efficiency (OEE), routing, BOM set up, Capacity & utilization database.
• Contribute to cost reduction/optimization projects
• Develop and implement strong continuous improvement culture
2. PRINCIPAL ACCOUNTABILITIES:
- Determines project requirements by extracting them from business master data, ERP systems, OEE and energy monitoring systems as well as from our current and future users through interaction and research.
- Identify and create business processes, which is formalized set of tasks and activities that helps accomplish specific business objectives.
- Developing and measuring standard metrics, diagramming the flow, including inputs and outputs of a business process, identifying opportunities for improvement.
- Implement advanced strategies for gathering, reviewing and analysing data requirements.
Key Accountabilities
• Clearly defines program objectives and scope.
• Secures employee commitment for proactive change management.
• Evaluates and prioritizes potential improvements based on gains and required effort.
• Establishes a clear and well-articulated implementation plan.
• Establishes criteria for the project's success and prepares a sound statement of constraints.
• Realistically defines specific project charters.
• Resolves technical problems: e.g., formulation, equipment, product, interpretation of regulations, resource availability.
• Implements Key performance indicators (K.P.I's) and establishes focus groups.
• Regularly monitors the implementation of solutions to achieve objectives and expected benefits. Responsible for cost saving initiatives.
• Continuous improvement utilizes all team members in Continuous Improvement Efforts
• Conducts a detailed analysis of the current situation and accurately describes the issues.
• Identifies available resources: people, materials, finances, etc.
• Clearly identifies Project Delivery Team (PDT) members and associates, and clarifies their roles and responsibilities
• Maps out in detail the desired situation.
• Analyses and identifies gaps.
• Clearly and rigorously defines methodology.
• Accurately analyses options as well as their impact and feasibility.
• Specifies obstacles and ways to overcome them from the perspective on continuous improvement.
• Stimulates ongoing optimizing of manufacturing equipment performance by utilizing expertise to analyse, monitor, troubleshooting and debottleneck current production processes to improve results.
• Developing roadmap anticipating upcoming new developments related to operational excellence.
• Defining, developing, and implementing dashboards for operations monitoring and executive reporting of continuous improvement results to MT.
• Liaise with manufacturing community on CI processes, to share best practices CI procedures.
• Principal contact to drive the LEAN work environment.
• Benchmark trends and practices, reviews practice and considers other people's suggestions.
• Accountable for staying aligned with the project sponsors and steering committees.
• Accountable for CI project execution in accordance with scope and deliverables.
• Accountable for the introduction, implementation, and compliance to new or revised CI activities and / or projects.
• Fostering operational improvements from inception to implementation with qualified benefits driving product cost down.
• Annual savings identifying in productivity, reject, waste and labour cost reduction.
• Engage in the continuous improvement effort to improve safety performance, product quality, unit cost, and employee performance, utilizing a participative team approach.
• The ability to apply sound business analysis techniques to a situation. Identify and adapt to new opportunities and find easier success. Helping business implement technology solutions in a cost-effective way by determining the requirements of a project or program, and communicate them clearly to stakeholders, facilitators, and partners.
• Developing technical solutions to business problems, or to advance the company's manufacturing performance efforts with defining, analysing, and documenting requirements.
• Involve in the design or review of test cases, process change requests, and manage a project's scope, acceptance, installation, and deployment.
• React quickly to rapidly changing conditions and processes by eliminating defects and enhancing quality while achieving and maintaining optimal levels of process performance.
• Improving the outcomes of various processes so that, by mapping all the inputs and outputs of a defined business process, the incumbent can recommend ways to improve efficiency, reduce cost and /or increase customer satisfaction. Working with front-line staff, identifying improvement opportunities, and coaching employees on how to work more efficiently. Participates in the implementation of the continuous-improvement program.
• Improves policies, procedures, and processes, manages the continuous-improvement program, advises, and assists front-line staff.
• Coordinate and work on the PPE Project with external consultants in coordination with Group.
• Contribute to the required Centurion CSR project, including coordination on the EMP (Environment Master Plan) with the region by working closely with local Sustainability Team.
• Contribute to improvements in cost, cash, quality, responsiveness, and time to market to support profitable growth of the business.
• Ensure definition and implementation of lagging and leading performance indicators and periodical reporting of actual performance against these indicators to facilitate timely decision taking.
• Ensure continuous improvement of Operating Efficiency (OEE), routing, BOM set up, Capacity & utilization database.
• Contribute to cost reduction/optimization projects
• Develop and implement strong continuous improvement culture
2. PRINCIPAL ACCOUNTABILITIES:
- Determines project requirements by extracting them from business master data, ERP systems, OEE and energy monitoring systems as well as from our current and future users through interaction and research.
- Identify and create business processes, which is formalized set of tasks and activities that helps accomplish specific business objectives.
- Developing and measuring standard metrics, diagramming the flow, including inputs and outputs of a business process, identifying opportunities for improvement.
- Implement advanced strategies for gathering, reviewing and analysing data requirements.
Key Accountabilities
• Clearly defines program objectives and scope.
• Secures employee commitment for proactive change management.
• Evaluates and prioritizes potential improvements based on gains and required effort.
• Establishes a clear and well-articulated implementation plan.
• Establishes criteria for the project's success and prepares a sound statement of constraints.
• Realistically defines specific project charters.
• Resolves technical problems: e.g., formulation, equipment, product, interpretation of regulations, resource availability.
• Implements Key performance indicators (K.P.I's) and establishes focus groups.
• Regularly monitors the implementation of solutions to achieve objectives and expected benefits. Responsible for cost saving initiatives.
• Continuous improvement utilizes all team members in Continuous Improvement Efforts
• Conducts a detailed analysis of the current situation and accurately describes the issues.
• Identifies available resources: people, materials, finances, etc.
• Clearly identifies Project Delivery Team (PDT) members and associates, and clarifies their roles and responsibilities
• Maps out in detail the desired situation.
• Analyses and identifies gaps.
• Clearly and rigorously defines methodology.
• Accurately analyses options as well as their impact and feasibility.
• Specifies obstacles and ways to overcome them from the perspective on continuous improvement.
• Stimulates ongoing optimizing of manufacturing equipment performance by utilizing expertise to analyse, monitor, troubleshooting and debottleneck current production processes to improve results.
• Developing roadmap anticipating upcoming new developments related to operational excellence.
• Defining, developing, and implementing dashboards for operations monitoring and executive reporting of continuous improvement results to MT.
• Liaise with manufacturing community on CI processes, to share best practices CI procedures.
• Principal contact to drive the LEAN work environment.
• Benchmark trends and practices, reviews practice and considers other people's suggestions.
• Accountable for staying aligned with the project sponsors and steering committees.
• Accountable for CI project execution in accordance with scope and deliverables.
• Accountable for the introduction, implementation, and compliance to new or revised CI activities and / or projects.
• Fostering operational improvements from inception to implementation with qualified benefits driving product cost down.
• Annual savings identifying in productivity, reject, waste and labour cost reduction.
Yêu cầu
• Strong background in Engineering & TPM/LEAN. Strong analytical and synthesis skills.
• Saving & improvement projects track proven. Continuous-improvement certification at the Green- or Black-Belt level (an asset).
• Five to ten years of experience in the FMCG manufacturing or another regulated field. Methodical and rigorous work habits (safety- and quality driven while focused on productivity).
• Bachelor's Degree from University is required, Engineering is preferred / MBA preferred
• Ability to communicate with all levels of organization.
• Ability to weigh and manage priorities.
• Flexibility and diplomacy in interpersonal relationships.
• Ability to influence decision- making.
• Organizational skills and ability to multitask (work on several projects at once).
• Proficiency in commonly used and specialized software e.g., Microsoft Office Suites.
• Willing to travel for the company as required by the business (occasionally not frequent).
• Delivers on time.
• Engaging Leadership - Exert influences, think strategically, out of the box, analytical abilities,
seize the opportunity.
• Taking people with you/inspiring people - lead yourself/lead others, drive collaboration, coaching, knowledge
transfer, inspire confidence.
• Problem Solving -can do attitude, implement solutions, policy deployment, strive for outstanding results.
• Overcoming the odds/ obstacle - being agile, show resilience, think creative, crisis manager
• Saving & improvement projects track proven. Continuous-improvement certification at the Green- or Black-Belt level (an asset).
• Five to ten years of experience in the FMCG manufacturing or another regulated field. Methodical and rigorous work habits (safety- and quality driven while focused on productivity).
• Bachelor's Degree from University is required, Engineering is preferred / MBA preferred
• Ability to communicate with all levels of organization.
• Ability to weigh and manage priorities.
• Flexibility and diplomacy in interpersonal relationships.
• Ability to influence decision- making.
• Organizational skills and ability to multitask (work on several projects at once).
• Proficiency in commonly used and specialized software e.g., Microsoft Office Suites.
• Willing to travel for the company as required by the business (occasionally not frequent).
• Delivers on time.
• Engaging Leadership - Exert influences, think strategically, out of the box, analytical abilities,
seize the opportunity.
• Taking people with you/inspiring people - lead yourself/lead others, drive collaboration, coaching, knowledge
transfer, inspire confidence.
• Problem Solving -can do attitude, implement solutions, policy deployment, strive for outstanding results.
• Overcoming the odds/ obstacle - being agile, show resilience, think creative, crisis manager
Quyền lợi
Attractive package
Good training courses
Company bus
Good training courses
Company bus
Thông tin khác
Ngày Đăng Tuyển
15/09/2023
Cấp Bậc
Trưởng phòng
Ngành Nghề
Sản Xuất, Thực phẩm & Đồ uống, Hàng tiêu dùng
Lĩnh vực
Hàng tiêu dùng
Kỹ Năng
Engineering, Lean Projects, FMCG, Project Management, Manufacturing Operations Management
Ngôn Ngữ Trình Bày Hồ Sơ
Bất kỳ
15/09/2023
Cấp Bậc
Trưởng phòng
Ngành Nghề
Sản Xuất, Thực phẩm & Đồ uống, Hàng tiêu dùng
Lĩnh vực
Hàng tiêu dùng
Kỹ Năng
Engineering, Lean Projects, FMCG, Project Management, Manufacturing Operations Management
Ngôn Ngữ Trình Bày Hồ Sơ
Bất kỳ
Thông tin chung
- Ngày hết hạn: 15/10/2023
- Thu nhập: Thương lượng
Giới thiệu công ty
Xem trang công ty
Công Ty TNHH Perfetti Van Melle Việt Nam là 1 trong 35 công ty con của tập đoàn Perfetti Van Melle - tập đoàn sản xuất bánh kẹo hàng đầu thế giới, có trụ sở đặt tại Lainate (Italia) & Breda (Hà Lan).
Chúng tôi là công ty liên doanh giữa tập đoàn Perfetti và Công ty thực phẩm Sài Gòn, nhằm tạo ra các sản phẩm và thương hiệu giàu trí tưởng tượng như kẹo, chewing gum cao cấp đang được ưu chuộng tại thị trường VN bao gồm: Alpenliebe, Golia, Cofitos, Mentos, Happydent, Big Babol, Chupa Chups .
Sứ...
Chúng tôi là công ty liên doanh giữa tập đoàn Perfetti và Công ty thực phẩm Sài Gòn, nhằm tạo ra các sản phẩm và thương hiệu giàu trí tưởng tượng như kẹo, chewing gum cao cấp đang được ưu chuộng tại thị trường VN bao gồm: Alpenliebe, Golia, Cofitos, Mentos, Happydent, Big Babol, Chupa Chups .
Sứ...
Quy mô công ty
Từ 1000 - 5000 nhân viên
Việc làm tương tự
Công ty TNHH Crystal Elegance Textiles Việt Nam
Cạnh tranh
10/03/2025
Bình Dương
Bệnh viện đa khoa Vạn Phúc 2
40 Tr - 60 Tr VND
31/01/2025
Bình Dương
hỗ trợ doanh nghiệp
Giải thưởng
của chúng tôi
Top 3
Nền tảng số tiêu biểu của Bộ
TT&TT 2022.
Top 15
Startup Việt xuất sắc 2019 do VNExpress tổ chức.
Top 10
Doanh nghiệp khởi nghiệp sáng tạo Việt Nam - Hội đồng tư vấn kinh doanh ASEAN bình chọn.
Giải Đồng
Sản phẩm công nghệ số Make In Viet Nam 2023.